Контролът на качеството е важен в почти всяка индустрия. Той гарантира, че всеки излизащ от завода продукт е с най-високо качество и същият като всички …
Автомобилната индустрия носи огромна отговорност да гарантира безопасността и удовлетвореността на превозните средства за милиардите потребители, които пътуват по пътя всеки ден. Очаква се автомобилните части да имат нулеви дефекти, без изключение. Некачествените продукти могат да застрашат живота и да навредят на репутацията на марката, маржовете на печалба и способността да изпълняват договорните задължения. Производителите, вносителите и търговците на дребно, участващи в производството на автомобилни части, трябва да прилагат строга програма за управление на качеството.
Съответствието на всяка автомобилна част е от решаващо значение за безопасността и ефективната функционалност на крайния продукт. Всичко от механични компоненти, електроника, двигател и неговите компоненти, батерии, лагери, спирачки, колела, кормилно управление, ауспуси, столчета за кола и батерии е също толкова важно, колкото каросерията на автомобила, боята и лепилата, осветлението и аксесоарите. Това означава, че контролът на качеството и проверката на качеството са важни, за да се гарантира, че всяко парче е безопасно, за да бъде част от превозното средство. Веригата на доставки на автомобилни части е както високоспециализирана, така и силно глобализирана. Автомобилните батерии и мехатроника идват предимно от по-напреднали производствени региони или страни като Европа, Китай и Тайван. Лагерите, каросерията и електрониката идват от производствените региони и страни, които имат по-напреднала верига на доставки за специфични компоненти като Югоизточна Азия, Източна Европа Китай и Тайван.
Значението на контрола на качеството
Защо контролът на качеството е толкова важен в автомобилостроенето?
За начало- запазва разходите. Инвестирането във висококачествени продукти може да изглежда скъпо, но в дългосрочен план може да ви спести пари. Продукт, който няма контрол на качеството, особено в автомобилната индустрия, може да предизвика скъпо изземване. Продуктите, които са опасни, могат да причинят автомобилни катастрофи и да бъдат опасни за водачите.
Контролът на качеството може също да открие проблеми, преди продуктът да бъде пуснат на пазара за потребителите, което води до по-добри версии. Той може да гарантира, че тези продукти отговарят на индустриалните стандарти – за някои компоненти, като системи за отработени газове и емисии, е необходимо да се спазват правилните стандарти.
VW научи този урок от първа ръка през 2015 г. когато беше открито, че автомобилите, продавани в Америка, са оборудвани с устройство за режим, което кара компютъра да мисли, че е в рамките на нормите за емисии. VW беше ударен с огромни глоби както в Европа, така и в САЩ и компанията трябваше да плати, за да поправи всеки автомобил. Контролът на качеството в автомобилната индустрия е от съществено значение, тъй като автомобилите са изначално опасни, ако не са правилно конструирани с добър контрол на качеството.
ПОДХОД ЗА КОНТРОЛ НА КАЧЕСТВОТО НА АВТОМОБИЛНИТЕ ЧАСТИ
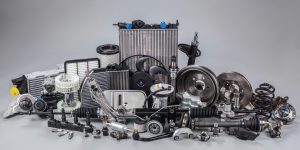
Някои тестове на автомобилни части изискват контролирана среда, за да се анализира тяхното съответствие със стандартите и разпоредбите на различните държави на местоназначение. Инспекторите на събират продукти онлайн и ги изпращат в акредитирана лаборатория за тестване.
Широкият опит в контрола на качеството на автомобилните части и водещият софтуер за управление на качеството могат да осигурят още по-голяма стойност.
Основни тестове, извършени по време на проверка на автомобилни части
|
|
Основни тестове на автомобилни части, извършвани в лаборатория:
|
|
|
Наличието на правилните инструменти
Автомобилният контрол на качеството е свързан с наличието на подходящите инструменти за работата. Тези инструменти ще варират малко в зависимост от точния продукт, който се произвежда, но има няколко основни инструмента, които всяко автомобилно съоръжение може да използва, за да подобри своя план за контрол на качеството. Тези инструменти включват анализ на режим на повреда, статистически контрол на процеса и анализ на измервателна система.
Анализът на режима на повреда позволява на съоръжението да анализира производствения процес и да прогнозира възможни точки на повреда. След като бъдат открити тези точки на повреда, могат да бъдат въведени контрамерки, за да се предотврати тяхното възникване по време на производството.
Процесите на статистически контрол се използват за контрол на качеството в почти всяка индустрия. Те използват статистически данни за контрол и подобряване на производствените процеси. Те трябва да бъдат леко променени, за да отговорят на специфичните нужди на автомобилната индустрия.
И накрая, анализ на измервателната система не се прилага към конкретен продукт, а към оборудването, което се използва за измерване и анализ на продуктите, преди те да станат достъпни за пускане на пазара. Тази стъпка гарантира, че измерванията, които се извършват, са точни, което позволява оборудването да се използва за контрол на качеството без прекалено голямо отклонение между партидите.
Изборът на правилните инструменти по време на производството също е важен за контрола на качеството. Наличието на правилната пясъчна шкурка за работа по каросерията, например, може да означава разликата между гладък завършен продукт и четвърт панел с вихри върху него, които се показват дори през боята.
Подобряване на автомобилния контрол на качеството
Какво могат да се направи, за да се подобри контрола на качеството? Започнете със създаване на качество на културата. Всички, от работника с най-нисък опит до най-високия мениджър, трябва да са фокусирани върху създаването на качествен продукт. Това посвещение включва провеждане на политика на отворени врати, при която работниците не се страхуват да поставят на вниманието на хората над тях производствени проблеми или проблеми с качеството.
Ако използвате доставчици, работете в тясно сътрудничество с тях, за да сте сигурни, че мерките им за контрол на качеството се привеждат в съответствие с вашите собствени. По този начин продуктите, които идват от други съоръжения, ще отговарят на вашите стандарти за качество, без да изискват ремонт или модификация, спестявайки както време, така и пари в дългосрочен план.
Приемете нови технологии, когато станат достъпни. Една от нововъзникващите тенденции е използването на добавена реалност – цифрови конструкции, проектирани на реални места – за подобряване на контрола на качеството. В някои случаи дори ръчните проверки за контрол на качеството могат да бъдат подобрени чрез добавяне на добавена реалност. Въпреки че тази практика все още не е широко възприета, тя представлява интересна нова опция за компании, които искат да подобрят своите мерки за контрол на качеството.
Освен това създайте изчерпателни контролни списъци за контрол на качеството, които могат лесно да се следват. Поддържайте всеки списък с правилния продукт през целия процес, за да намалите шанса дадена стъпка да бъде пропусната или забравена.
Контролът на качеството е съществена част от автомобилната индустрия – тази, която не можете да си позволите да пренебрегнете. Без значение какви стъпки предприемате, за да подобрите процеса си на контрол на качеството, уверете се, че те са универсално приети – ако екип или двама се придържат към старите QC процеси, може да доведе до безброй проблеми в дългосрочен план. Отделете време за подобряване на тези процеси и ще ви бъде по-лесно да използвате продукти с постоянно високо качество и идеални за непрекъснато променящата се автомобилна индустрия.
КАКВО ПРЕДСТАВЛЯВА КОНТРОЛЕН СПИСЪК ЗА КОНТРОЛ НА КАЧЕСТВОТО?
Вносителите често искат да знаят кой е най-добрият начин да се изяснят техните продуктови изисквания, както на техния доставчик, така и на всеки инспектиращ персонал, който може да провери поръчка преди изпращане.
За тази цел най-често служи контролен списък за ефективен контрол на качеството (QC). А за контрол на качеството списъкът е в основата на писмено ръководство за съдържанието на продукта, опаковки, цветове, баркодове, външен вид, възможни дефекти, функции и специални изисквания. Понякога се нарича „лист с критерии за проверка“ или контролен списък за проверка.
Контролните списъци за подобни продукти често споделят общи критерии за проверка. Но обикновено всеки вносител често има специфични изисквания за своя продукт. Ето защо е важно за вносителите да приспособят контролния списък за контрол на качеството според своите уникални нужди.
ПЕТ КЛЮЧОВИ ЕЛЕМЕНТА НА ЕФЕКТИВЕН КОНТРОЛЕН СПИСЪК ЗА КОНТРОЛ НА КАЧЕСТВОТО
Има пет елемента от контролния списък за контрол на качеството, които са жизненоважни. Някои са по-очевидни за вносителите, докато други често са непознати или пренебрегвани. Петте елемента включват:
- Изисквания към продукта
- Изисквания към опаковката
- Тестове и проверки на място
- Класификация на дефекти
- Сътрудничество между вносителя, доставчика и персонала
Какви са основните инструменти за качество
Основните инструменти за качество са дефинирани като пет допълнителни техники и / или методи, които подкрепят очакванията. Тези инструменти са документирани отделно чрез публикуването на пет ръководства, достъпни чрез Action Group за автомобилна индустрия (AIAG). Традиционните пет основни инструмента са изброени в техния ред на използване при проектиране на продукти или процеси:
- Разширено планиране на качеството на продукта
- Анализ на режима на отказ и ефекти
- Анализ на измервателни системи
- Статистически контрол на процесите
- Процес на одобрение на част от продукта
Какво е разширено планиране на качеството на продукта
Разширеното планиране на качеството на продукта е набор от инструменти и техники, които се използват за осигуряване на качеството на продукта чрез съобщаване на изисквания, спецификации и рискове. Има пет раздела или фази на контрол с допълнителна фаза на въвеждане:
- Предварително планиране или въвеждане
- Фазата на предварително планиране подкрепя проучването на научените уроци и установяването на предположения, които се използват за осигуряване на успех.
- Планиране и дефиниране
- Установяват се целите за надеждност, качество и дизайн, свързващи Гласа на клиента (VOC) с писмени и постижими изисквания.
- Концепциите за предварителен дизайн се използват за създаване на спецификация, улесняваща планирането на продукти и процеси.
- Продуктов дизайн и разработка
- Фазата на дизайна на продукта вмъква инструменти за надеждност и качество в сроковете на проекта, предназначени да открият технически рискове. Техническият риск е заместителят на неуспеха. Действията, насочени срещу идентифицирани рискове, са от полза за предотвратяване на повреда на продуктите както при тестване, така и при употреба.
- Анализ на режима на отказ на проектиране и ефекти е един от многото инструменти, който може да идентифицира рисковете за превантивни действия.
- Специалните характеристики са усъвършенствани и предоставени на производствените и монтажни дейности.
- Проектиране и разработване на процеси
- Проектирането на производство и монтаж, също е източник за неуспех. Ако не бъдат проверени, могат да доведат до недоволни клиенти, и закъснели доставки.
- Режим на отказ на процеса и анализ на ефектите е един инструмент, използван за идентифициране на областите на риск, изискващи действия преди ангажимента за изграждане на инструментариум и оборудване.
- Всички специални характеристики се оценяват за превантивни действия, като се използват доказателства за грешки, статистическа стабилност / способност или проверка на грешки.
- 5.Валидиране на продукти и процеси
- Целта на раздела е да представи доказателства, че дейностите по планиране са били продуктивни.
- Анализът на системите за измерване се използва, за да се гарантира, че системата за оценка и измерване може да определи целостта на продукта.
- Първото пробно производство се използва за определяне на качеството чрез оформяне на размерите и използване на Статистически контрол на процесите. Специалните контроли и методи за контрол са валидирани и документирани в плана за контрол.
- Документацията за процеса на одобрение на производствената част може да бъде представена за одобрение в края на раздел 4.
- Оценка на обратната връзка и коригиращи действия
- Продуктът или услугата вече са в пълно производство. Научените уроци, заснети от всяка фаза, се поставят в извличаща се база данни за бъдещи справки.
- Опитът, считан за полезен, се използва за установяване на нови нива на стандартна работа и се споделя в цялата организация.
- Вътрешното и външното наблюдение на изпълнението за доставка, качество и непрекъснато подобряване (например намаляване на номера на приоритетния риск) следва процедурните, изисквания.
- Когато възникне неуспех, се използват анализ на основната причина и осем дисциплини за решаване на проблеми (8D) , за да се намери основната причина с намерението да се коригира трайно.
Какво е режим на отказ и анализ на ефектите
Анализът на режима на отказ и ефекти е структуриран подход, който идентифицира потенциалните режими на отказ и произтичащите от тях ефекти, като ги свързва с потенциални причини за отказ. За всяка комбинация се определя ниво на технически риск. Когато се счита, че рискът е твърде голям за продукта или процеса, който се изследва, се идентифицират действия за намаляване на риска. Също се преглеждат техниките за тестване и оценка, които могат да определят целостта и надеждността на дизайна на продукта или качеството на продукта.
Оценката на риска и предприемането на смекчаващи действия е от полза чрез предотвратяване на неуспех, преди да е изпитан. Използват се няколко фактора:
- Тежест: Обозначава колко опасност или недоволство съществува за неуспеха и произтичащия ефект
- Възникване: Оценка на вероятността за отделни причини, които са свързани с режима на повреда
- Откриване: Класиране на ефективността на улавяне или на конструктивен дефект преди пускането на дизайна, или способността на контрола на процеса при предотвратяване или откриване на дефектно състояние, което не отговаря на проектното намерение
- Критичност: Комбинацията от тежест и поява, което може да означава неприемлив риск
Какво е анализ на измервателните системи
Анализът на системите за измерване е експериментален процес, който определя жизнеспособността на техниката за оценка / измерване за използване върху специфична характеристика на частта. Необходимостта от вземане на качествени решения е най-важният аспект на осигуряването и контрола на качеството. Ако избраната система за измерване има твърде много вариации или е нестабилна, може да бъде одобрен неприемлив продукт, което да доведе до недоволство на клиентите или по-лошо. И обратно, приемливият продукт може да бъде отхвърлен, като се окаже допълнителен натиск върху организацията да реагира на състояние, което не изисква действие. Грешката в измервателната система е неизбежна. Мнозина приемат, че измерването е абсолютно, което за съжаление не е вярно. Много пъти системата за измерване може да бъде напълно неприемлива и да изисква подмяна или значително подобрение.
Разглеждаме пет различни параметъра:
- Най-свързано с калибрирането, пасването е количеството на отклонението на измерване, получено от системата, между стандартно проследимо до организация по стандартизация (например Национален институт за стандарти и технологии или еквивалент)
- Линейност: Отнася се до разликата в очакваното отклонение на измерването в обхвата на измервателния уред или устройство
- Точността на устройството не остава една и съща през целия полезен обхват на измерване
- Стабилност: Способността на измервателния уред да осигури едно и също измерване на един и същ продукт, който се измерва във времето
- Измервателният уред не е стабилен, ако показва отклонение от предишни измервания на същата част
- Повторяемост: Казва се, че измервателната система е повторяема, ако един и същ оператор и измервателен уред, изследвани при същите условия, могат да повторят един и същ резултат
- Лошата повторяемост би означавало, че операторът използва същата част, измерва я и получава различен резултат от предишни измервания (при идентични условия)
- Възпроизводимост: Системата се счита за възпроизводима, ако множество оператори могат да получат еднакви или подобни показания на едни и същи части
Насоките за приемане се основават на два принципа:
- Процент грешка до толеранс: Общата вариация на смесената повторяемост и възпроизводимост, разделена на общия толеранс. Тази оценка се използва за валидиране на система за измерване първоначално.
- Процент грешка във вариацията: Общата вариация на смесената повторяемост и възпроизводимост, разделена на общата вариация на продукта / процеса.
Указанията за приемане са както следва:
- 10% грешка или по-малко
- Допустима грешка 10-30% в зависимост от фактори като разходи за измерване, тежест на ефекта от повреда или разходи за ремонт на измервателния уред
- Ако е по-голяма от 30%, измервателната система е неприемлива и изисква подобрение или подмяна
Какво е статистически контрол на процеса
Статистическият контрол на процесите (SPC) представлява колекция от статистически техники, предназначени да разберат поведението на системата. SPC използва основните статистически принципи на централна тенденция (средно, медиана и режим) и вариация (спред или стандартно отклонение). Изследваният процес ще разкрие дали той работи по стабилен и предсказуем начин или в контрол.
Контролни диаграми
Диаграмите за контрол обикновено се използват за обозначаване на модели, които могат да се различават от очакваните проценти на кривата. Когато се наблюдава модел, процесът е извън контрол и действията за разследване са често срещани. Диаграмите за контрол се разделят на две категории, променлива и атрибут. Диаграмите за променлив контрол използват данни, които, когато са нанесени на диаграмата, могат да бъдат интерпретирани. Диаграмите за контрол на атрибутите показват ефективността на набор от данни Go / No Go.
Диаграмите с променлив контрол обикновено се предлагат по двойки; една за централната тенденция и друга за разпространението. Всяка диаграма има линия, изчертана за измерване на централната тенденция и контролни граници, равноотстоящи линии от двете страни на централната тенденция. Контролните гранични линии се равняват на очакваното разпространение при ± 3 стандартни грешки въз основа на размера на извадката на групата или подгрупата.
Пробите се избират на определени честоти и двете точки, едната за централна тенденция, другата за разпространение, се начертават. Начертаните точки се оценяват заедно с до шест предишни точки. Стабилността на процеса се определя чрез следните критерии:
- Точка извън контролната гранична линия
- 7 точки подред от двете страни на централните линии на тенденция
- 6 или 7 точки в същата посока
- 7 точки подред, които прегръщат централната тенденция
Когато се използва този критерий, диаграмата може да посочи какво най-вероятно ще дойде след това. Извън контрол не се отнася до лош продукт, просто различен от предишния опит. Диаграмата може да показва състояние извън контрол, но при внимателно проучване анализаторът може да поиска да запази това и да установи нов най-добър случай.
Диаграмите за контрол на атрибутите изобразяват само условия, които са неприемливи. Извършват се действия за подобряване на нежеланото състояние. Диаграмите за контрол на атрибутите често са свързани с непрекъснато усъвършенстване, защото те могат да бъдат отлични визуални помощни средства за показване на напредъка.
ЗАКЛЮЧЕНИЕ:
Може би преди всичко друго, искам да подчертая, важността на наличието на задълбочен контролен списък за контрол на качеството, който да обхваща всички аспекти на един продукт. Не на последно място, трябва да подчертая,че основният проблем при резервните части за автомобили, не е във нивото на тяхното качество, а в неправилният им подбор, при изборът им при монтаж, както и ниското качество на извършваните ремонти, което произтичат от ниското ниво на компетентност при механиците.