Автомобилните покрития и процесите, използвани за покриване на автомобилни повърхности, са пример за авангарда на технологиите, които са в състояние да произвеждат трайни повърхности, надвишаващи очакванията на клиентите за външен вид, увеличаване на ефективността и спазване на екологичните разпоредби.Поради напредъка, насочен към разбирането на това как, защо, кога и къде на автомобилните покрития, напредъка в контрола върху капчиците и техните атрибути на отлагане, както и разработването на нови технологии и химикали за боядисване, цялостен и актуален преглед на автомобилните покритията и технологиите за покритие се считат за полезни за специалистите в областта на промишлеността и изследователите. Като цяло, критичните фактори за ефективност, които движат развитието и използването на модерни автомобилни покрития и технологии за покритие, са: а) естетически характеристики; б) защита от корозия; в) масово производство; г) разходи и екологични изисквания; и (д) външен вид и дълготрайност. Въпреки че относителното значение на всеки от тези фактори е спорно, усъвършенстването на който и да е за сметка на друг би било неприемливо. Фактът, че различни видове корозия засягат автомобилите, също означава, че се изискват различни решения.
Атмосферната корозия може да възникне, когато всяка метална повърхност на превозното средство влиза в контакт с въздух, съдържащ влага. Тънкият филм от влагата, отложена при определени условия е достатъчен, за да предизвика постепенното разпадане на стоманените повърхности. Дебелината на филма ще зависи от фактори като температура и налягане на околната среда, относителна влажност и наличието на соли.
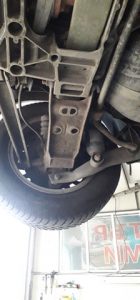
Корозията на пукнатината се отнася до електрохимични процеси, които протичат в затворени пространства, като уплътнения, фланци и пространства, пълни с отлагания. Този вид корозия е локализирана атака поради наличието на застоял разтвор или електролит.
Галваничната корозия се получава, когато два различни метала се поставят в електрически контакт. Единият метал може да корозира спрямо другия. Корозията на гайките и болтовете за съединяване на компоненти е един такъв пример.
Питингът е друга форма на локализирана атака, подобна на корозионната корозия. Обикновено се среща в иначе пасивни материали, при които пасивният оксиден филм, който защитава метала, се разгражда в резултат на химическа или механична атака. Хлорът в солената вода е много ефективен при разграждането на такива пасивни оксидни филми.
Антикорозионното покритие е ефективен начин за предотвратяване на ръждата и повредите, които може да причини, корозията върху превозните средства. Ако мислите да инсталирате тази важна защита на вашия автомобил, трябва да разберете различните методи, които се използват за нанасяне на антикорозионни покрития върху автомобила.
Защита от корозия

Автомобилните покрития са подложени на редица различни среди и ситуации през техния експлоатационен живот. Разграждането на покритието зависи от три основни фактора: формула на покритието, интензивността на околната среда или ситуацията и продължителността им. Излагането на ултравиолетово лъчение от слънце, топлина и влажност има дългосрочен вреден ефект с различна степен на интензивност в зависимост от климата и метеорологичните условия. Тези три фактора обаче могат да бъдат симулирани в контролирани, лабораторни изпитвания за атмосферни влияния, за да се оцени продължителността на живота на покритията. Често автомобилните покрития също са подложени на корозивни газове и микроорганизми; тези фактори на разграждане обикновено се пресъздават само в лабораторни тестове за специални ситуации на приложение. За да се потисне или премахне корозията, е необходимо да се придобие солидно разбиране за нея. Всички метали след производството или оформянето имат тенденция да търсят по-ниската си енергия, естествено състояние, което първоначално е било в рудата, от която произлиза. Тази тенденция се причинява от Закона за ентропията, т.е. , ниско енергийното състояние е на окислено, корозиращо състояние. В автомобилите корозията обикновено е резултат от електрохимични реакции, при които стоманата е потопена в подходящ електролит, като вода и пътна сол, и ще създаде някои локализирани аноди и катоди. Тогава настъпва анодно окисляване и катодна редукция, по време на което електроните преминават от анодите към катодите.
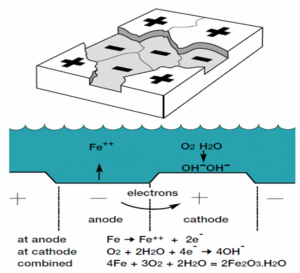
В резултат на анодното разтваряне в крайна сметка ще се случи перфорация в метала. Освен това, корозия може да възникне, когато два различни метала са в контакт в присъствието на електролит. Наричан биметална корозия или галваничен ефект, металът с по-нисък потенциал ще се превърне в анод с производството на електрони и свързани метални йони, а другият метал ще действа като катод. Факторите, които влияят на корозията, включват влажност, температура, различни замърсители на въздуха като хлор, серни окиси и азотни окиси и зимни соли за обезледяване на пътя. Тези фактори могат да доведат до няколко форми на корозия.
В търговската мрежа се предлагат редица ефективни системи за защита от корозия, най-често срещаната от които включва покритието на стомани с цинк. Той осигурява на основата устойчивост на корозия чрез катоден контрол, тъй като цинкът има някои характеристики, които го правят добре подходящ за изделия от желязо и стомана. Цинково покритие или поцинковане се извършва чрез различни методи, включително:
-
Пакетно поцинковане с горещо налягане : е процесът на потапяне на изработена стомана или желязо във вана с разтопен цинк. Желязото в стоманата металургично реагира с цинка и образува плътно свързано покритие от сплав.
-
Метализиране : става чрез разтопяване на цинков прах или цинкова тел в пламък или електрическа дъга и след това изпъкване на капчиците течен цинк чрез въздух или газ върху повърхността, която трябва да бъде покрита.
-
Боя с цинк: Боядисването с цинк, обикновено наричано от неправилното наименование „студено поцинковане“, е нанасянето с четка или спрей цинков прах, смесен с органични или неорганични свързващи вещества.
-
Непрекъснато поцинковане на листа : също е процес на горещо потапяне, но се прилага само върху стоманени листове, ленти и телове.
-
Електроплакиране : електрогалванизираните (галванизирани) покрития се създават чрез нанасяне на цинк върху стоманен лист и лента чрез електроосаждане.
-
Механично покритие: механичното цинково покритие се осъществява чрез пресоване на малки части в барабан с цинк и собствени химикали.
-
Поцинковане : по принцип е идентично с електрогалванизиране, тъй като и двете са процеси на електроразлагане. Въпреки това, цинковото покритие се използва на малки части като крепежни елементи, пружини и други елементи, а не върху ламарина.
Аспектите на дизайна, които влияят на устойчивостта на корозия, могат да бъдат разделени на следните.
-
Характеристики на стайлинг : именно на етапа на външно моделиране на глина на купето на автомобила може да се вземе решение за главното разделяне на панела, т.е. когато се планира действителната конфигурация на панела, която определя броя на ставите и свързаните шевове, всички от които са потенциални места за корозия на пукнатините.
-
Подсглобяване : при дизайна на сглобяването е важно да се избягва сложността, тъй като сложността неминуемо нарушава адекватното покритие на панелите с боя и восъци. Реалните опасни зони са допирни повърхности, които насърчават корозията на пукнатините и причиняват намалена дебелина на покритието.
-
Панел и дизайн : индивидуалните характеристики на панела трябва да включват отводнителни отвори, разположени в най-долния край на секцията в следващите възли.
Съвременни процеси за автомобилно покритие
Съвременните автомобилни методи за покритие се състоят от пет основни стъпки. Те включват следното:
Предварителна обработка: отстранява и почиства излишния метал и образуване на подходяща повърхностна структура, позволяваща свързване на защитен слой от корозия.
Следващата стъпка е електроосаждане (ED) на антикорозионния или предотвратяващ ръжда слой.
Уплътнител като поливинилхлорид (PVC) се прилага за антикорозия, премахване на течове на вода и минимизиране на струпването и вибрационния шум.
След това се нанася грунд за насърчаване на сцеплението между повърхността и основния слой; той също така придава по-гладка повърхност за следващи слоеве.
Накрая се нанасят горните слоеве, които включват основен слой и прозрачен слой; те осигуряват търсените повърхностни свойства, включително цвят, външен вид, блясък, гладкост и устойчивост на атмосферни влияния. За да бъдат лесно визуализирани външните повърхности на автомобила, петте основни стъпки на покритието създават слоеста структура. Тези покрития се нанасят в определен ред и имат различни материали и функции за защита или довършителни работи; също всеки слой се отнася до останалите и придава желания баланс на свойствата.
Предварителна обработка
Когато компонентите на ламаринените кутии на автомобила са заварени заедно, получената структура се нарича „бяло тяло“ (BIW). Първата последователност при подготовката на BIW за последващо покритие е предварителната обработка. Предварителната обработка се състои в почистване на повърхността на тялото, за да се отстранят остатъчните масла от процеса на щамповане и остатъци от заваряване чрез три първични процеса на потапяне на течността от обезмасляване, кондициониране и фосфатиране. Може да се използва и допълнително почистване за предварително третиране, което използва гореща вода с pH 9. Предварителната обработка помага на грунда да се свърже върху метала. При обработката на фосфати се прилага инертен слой метален фосфат, осигуряващ устойчивост на корозионно разпространение. Разтворът за обезмасляване се състои от алкални соли и повърхностно активни вещества и може да включва сода каустик, тринатриев фосфат и натриев карбонат. Повърхностно активните вещества са видове почистващи препарати за емулгиращи масла и смазочни материали на BIW. Зоната за обезмасляване обикновено се състои от най-малко две последователности, включително етап на разпръскване, известен като разграждане-обезмасляване (KOD) и потапяща последователност. Предимството на използването на тези две е, че значителна част от маслото и мръсотията ще бъдат отстранени от спрея под високо налягане, като по този начин се оставя сравнително по-нисък товар за почистване на потапящата серия.
Следващата последователност е повърхностното кондициониране (наричано още активиране), което създава места за нуклеиране за растеж на фосфатни кристали. Той увеличава броя на ядрата на кристализация на металната повърхност, които засилват свързващите механизми за последващата фосфатна последователност. При кондициониране обикновено се използва водна дисперсия на титанов ортофосфат с рН между 8 и 10. И накрая, течният разтворен фосфатен разтвор се състои от фосфорна киселина, фосфатни йони, нитратни йони, цинк и други двувалентни метални йони, водородни йони и ускоряващо съединение. Свободната киселина води до отделяне на водород, докато металните фосфатни йони се утаяват върху повърхността в кристална форма. Основната цел по време на фосфатирането е да се нанесе тънък, плътен и равномерен конверсионен слой върху почистената и подготвена метална повърхност.
Галваничното отлагане (ED)
Металното покритие и рамите на автомобилите са с покритие за предотвратяване на корозия, докато други области като покрива не са устойчиви на ръжда. Когато не са покрити, за да се предотврати корозия, структурните метали (или други материали) се грундират преди нанасяне на допълнителни покрития.
SCGA разтвор за (ED) със състав 90% Zn – 10% Fe (GA материал) е основното покритие, използвано в съвременните автомобили за предотвратяване на корозия. В сравнение с разтвора на SGC, т.е. GI материал, със 100% Zn по време на (ED), GA материалът свежда до минимум газовият щифт ED (дефекти в качеството на боята) и увеличава максимално ефективността на заваряване на място; процесът на SGC все още се използва в Европа. Методът за защита от корозия SCGM е бил използван в предишните десетилетия и дава възможност за минимизиране на щифта на ED.
Електроосаждащият слой или E-coat осигурява защита от ръжда и корозия и е представен за първи път през 60-те години. Оттогава използването му нараства с бързи темпове. Днес това е най-конвенционалният процес на покритие, използван при производството на превозни средства.
Дебелината на фолиото за E-coat също варира през този период от време. Дебелините започват от 25 цт и остават така до 1976 г., когато се приема катодния процес и се установява дебелина от 18 цт; тя остава при тази стойност до 1984 г., когато дебелината на филма е увеличена до 35 цт. Този сравнително дебел филм се използва до 1992 г., когато дебелините на покритието на Е-покритието са намалени до текущата стойност от 20 µm. Разтворът на E-coat се състои от смес от смола, свързващо вещество, паста, съдържаща пигментите и разтворител. По време на анодно електроосаждане металните части се зареждат положително, докато боята е заредена отрицателно; тъй като малки количества метални йони мигрират във филма за боя, това ограничава експлоатационните свойства на покритието. Следователно, анодното покритие се използва главно за интериора и предлага отличен контрол на цвета и блясъка. При катодно електроосаждане металната част се зарежда отрицателно, докато боята е положително заредена. За разлика от анодния процес, катодният процес намалява количеството желязо, което може да влезе във филма за боя. Процесът на E-coat се счита за относително екологичен. PH на разтворителя в ED резервоара е мярка за баланса на киселинни и каустични компоненти в резервоара. Балансът е доминиран от функционалните групи в смолата и неутрализиращите агенти. Намаленото рН в катодния ЕД резервоар намалява дебелината на филма, така че трябва да се прилага по-високо напрежение с опасност от разрушаващи ефекти. PH може да бъде повлиян от химикалите за предварително третиране което е вредно. В такъв случай, проводимостта и отклонението на pH към стойности извън спецификацията и корекциите трябва да се извършват чрез попълване на ултрафилтрат с дейонизирана вода (DI).
E-покритието включва потапяне на автомобилни тела в разтвора на покритието и преминаване на електрически ток през тялото и разтвора на течната ED боя. Поради заредения характер на този процес на нанасяне на покритие, ED боята прониква на места, където спрей не би достигнал. ED боята се насърчава да се свързва с металния субстрат и се получава равномерна дебелина на покритието. Резултатът е неразтворим, отложен слой с много високо съдържание на твърди вещества и твърдо прилепване към предварително обработеното тяло. По време на работа в резервоара за електроосаждане се подава смес от смола, свързващо вещество и паста, съдържаща пигментите. Корпусът на автомобила се спуска в резервоара и се прилага електрически ток; разтворът в резервоара се състои от 80% -90% дейонизирана вода и 10% -20% твърди частици (състоящи се от смола, свързващо вещество и пигмент). Дейонизирана вода действа като носител на твърдите части на боята, които са под постоянно разбъркване. Смолата е основата на крайния филм за боя и осигурява корозия, устойчивост и здравина. Пигментите се използват за осигуряване на цвят и блясък. За да контролирате работата на боята по време на катодното E покритие, от съществено значение е продухването на боята и регулирането на количеството на приложеното напрежение. С нарастването на дебелината покритието става все по-изолиращо, което води до забавяне на процеса на отлагане.
След E-покритието автомобилното тяло влиза в пещ за печене, в която загряването и поддържането при температура от 160 ° C в продължение на 10 минути предизвиква втвърдяване на филма, за да се постигнат максимални свойства на работа. Температурата и времето за загряване на фурната засилват предимно устойчивостта на адхезията на филма към тялото; защитата от корозия се влияе по-малко от тези условия. Тъй като грапавостта на повърхността влияе върху гладкостта и блясъка на горното покритие, обикновено се нанася шлифоване на повърхността, за да се отстранят дефектите, преди тялото да влезе в следващата стъпка на нанасяне. Често срещано предизвикателство в текущия процес на E-покритие е това на водни петна, които замърсяват покритите повърхности. Тези петна могат да се появят на изсушената на въздуха повърхност, ако капки вода от транспортера или други източници паднат върху тялото, особено ако водата в резервоарите не е дейонизирана правилно и има висока проводимост; водните петна обикновено са остатък от нежелани йони във водата и ще създадат проблеми при последващи приложения на покритието и тяхното прилепване и външен вид. Ако има водни петна, те трябва да бъдат отстранени чрез шлифоване. Следователно е необходимо да се използва добре дейонизирана вода и да се следи рутинно нейната проводимост. Алтернативно операторите също добавят повърхностноактивни вещества или ултрафилтрати към зоната за изплакване с вода, за да премахнат или управляват водни петна.
Материали, устойчиви на ръжда: Уплътнител / PVC
Третата стъпка е покритие и запечатване на шевове, като се използва PVC (поливинилхлорид) и уретан. Това уплътняване има множество цели.Уплътнителят се нанася около и отвътре на вратите, багажникът и върху външната и вътрешната страна на металните фуги и външната зона на задното колело; нанасянето на уплътнителя се извършва ръчно или с роботи и предотвратява навлизането на въздух и вода и инхибира образуването на ръжда. В последно време PVC и акрил / уретанови уплътнители също се използват за да се придаде шумоизолация. Шумът и вибрациите се предават от двигателя, задвижващия механизъм, системата за окачване, шума на пътя на гумите и потока на въздуха, а уплътнителите намаляват предаването на шум в купето на автомобила. Покритието на долното тяло осигурява също антикорозионна и защитна струга; обикновено се осъществява с помощта на роботи, оборудвани с безвъздушни пръскачки.
Грунд
Четвъртият етап на покритие е нанасянето на грундираща повърхност или просто грунд. Той може да бъде воден, разтворен или на прах. Основната причина за нанасяне на грунд до 1990 г. е да се подобри устойчивостта на атмосферни влияния, външния вид и устойчивостта на струпване. От 1990 г. праймерите са разработени в материали, пренасяни с разтворители и вода, и прахове (изрично за намаляване на количеството на летливи органични съединения (ЛОС), изхвърлени в атмосферата или съоръжения за улавяне на замърсители). Днешните грундове трябва да подобрят адхезията между E-coat и топ лак, да осигурят защита и да подобрят външния вид на боята и също така да бъдат екологично съвместими с нормите за емисии. Грундът запълва и изглажда дребните несъвършенства и драскотини, които могат да бъдат създадени по време на предходни стъпки и от междинното шлифоване, използвани за отстраняване на малки несъвършенства. Освен това повечето автомобилни каросерии имат повърхностни несъвършенства, които възникват при операциите по пресоване, щамповане и заваряване, като тези дефекти обикновено се подчертават по време на стъпката на ED. Следователно, въпреки че основната цел на грунда е да действа като изравнител, който създава по-гладка завършена повърхност, той също така осигурява допълнителна защита срещу корозия и увеличава максимално сцеплението между него и Е-покритието и основния слой; по този начин грундът увеличава трайността на боята. Обаче, тъй като операциите за пресоване и щамповане стават по-сложни и създават по-малко несъвършенства, характеристиките на изглаждането на грундовете стават по-малко важни. Грундният слой е важен за устойчивостта на каменни стърготини. В същото време е необходимо добро сцепление на горния слой с грундиращата повърхност, за да се гарантира минимално отклонение от визуалния вид. Следователно е обичайно да се включват подходящи цветове в грундове, които са съвместими с горния слой, маскирайки щети върху горното покритие.
Използваният тип грундираща повърхност също влияе върху оперативните аспекти на този етап на покритие. По време на разработването на грундове те обикновено се тестват за повърхностна твърдост и еластичност, както и за техните адхезивни свойства върху ЕД покритието и материалите за основно покритие. От решаващо значение е да се тества повърхностната твърдост, тъй като тя играе значителна роля за съвместимост с мерки за коригиране на дефекти като шлифоване. Еластичността осигурява индикация за потенциалната способност за защита от каменна стружка на грундираната повърхност. Адхезията към ED покритията и базовите покрития също е от съществено значение за минимизиране или предотвратяване на корозия и за постигане на оптимално покритие на повърхността.
Освен механичните и адхезивните свойства на грундовете трябва да се оцени тяхната химическа реактивност на ултравиолетово (UV) излъчване и екстремни атмосферни условия като висока влажност и ниски или високи температури, тъй като автомобилите са постоянно изложени на тези условия по време на жизнения си цикъл. Този тип проблеми са важни за собствениците, които след като имат автомобил известно време, могат да видят значително влошаване на боята като знак за лошото качество на автомобила. Следователно производителите на грундове тестват гладкостта на грундиращите покрития, за да гарантират тяхната приложимост и външен вид върху горния слой. Гладкостта на покритието, получена чрез метод за сканиране на вълни, генерира стойности в скали на къси и дълги вълни.
Реологията на повърхността с течен грунд е необходима за оценка на неговата ефективност. Реологията се отнася до характеристиките на потока, чиято мярка е вискозитетът, определен от скоростта на срязване с помощта на реометър. Доста високото ниво на вискозитет предотвратява образуването на утайка по време на съхранение на грунд, но прилагането на спрей изисква вискозитет толкова нисък, колкото е възможно, за да се оптимизира пулверизацията. Ако обаче вискозитетът е твърде нисък, ще се получи провисване на филма върху вертикални повърхности. Дори за идеален вискозитет, провисване по вертикални повърхности ще се случи, ако грундът е твърде дебел. За праховите покрития разпределението на размера на частиците е критичен фактор. Високото съдържание на фин прах ще повлияе значително на ефекта на ван дер Ваалс -привличане между частиците, в резултат на което частиците се агломерират и станат невъзможни или трудни за разпръскване. Операциите за грундиране на покритие в автомобилна инсталация обикновено се извършват на три етапа: вътрешно покритие, външно покритие и след това втвърдяване във фурна. Ръчно боядисване със спрей се използва за вътрешното покритие на вратите, двигателното отделение и багажното пространство. Някои от тези области не се напръскват с основен слой. Важно е цветът на грунда да съвпада с основния слой, за да може да придава равномерни облицовки между вътрешните и външните покрития. Дебелината на филма на вътрешния слой е близо 20 μm. Боядисването на грундиране на екстериора се извършва след завършване на вътрешното грундиране, обикновено с помощта на въртящи се апликатори, за да се образува филм с дебелина 25-40 mm. Впоследствие грундът се втвърдява чрез преминаване на тялото през фурна при 140 ° С за 30 минути.
Горен пласт
Последната стъпка в процеса на покритие на тялото е нанасянето на топ лак, който се състои от два слоя – основен и прозрачен. Основното покритие съдържа основния оцветяващ пигмент, а прозрачният слой осигурява защитно покритие срещу въздействието на околната среда, корозията и разграждането на ултравиолетовата светлина, насърчава ненадминатото задържане на цвета и осигурява гладко, незамърсено и равномерно покритие. Тялото първо се покрива с воден или с разтворител основен слой. Ако производителят използва метод „мокро върху мокро”, тогава прозрачният слой се нанася върху основния слой след кратко изпускане, преди да се втвърди във фурна. При липса на мокър върху мокър слой, основното покритие се втвърдява преди нанасянето на прозрачния слой. Независимо от кой процес се използва, типичните времена на термично втвърдяване и температури са съответно 30 до 40 минути при 125 ° С . Нанасянето на тези крайни покрития се извършва в кабини за пръскане, които включват: системи за обработка на въздуха за контрол на температурата, влажността и чистотата; оборудване за заснемане на боя и VOC. Климатичната система съдържа филтрираща среда за контрол на прах и мръсотия. Водата и големият въздушен поток се използват за улавяне на частици боя във мокри скрубер. Контролираният въздушен поток в кабината транспортира частиците на боята в оборудването за улавяне в долната част на кабината. Силата и посоката на въздушния поток, ефективността на филтрирането и характеристиките на покривното оборудване определят не само общата ефективност на работата на покритието, но и качеството на крайния завършек. Трябва да се отбележи, че напредъкът в технологиите за сух скрубер е водещ в отрасъла при замяната на мокри скрубер със сухи скрубер. Сухите почистващи препарати предлагат значително намаляване на използването на вода и емисиите на въглероден диоксид и прахови частици.
Basecoat
Като част от топ лака, основният слой е третият слой, добавен към колата след грунда и преди прозрачния слой. Придава цвета на автомобила; днес са известни приблизително 40 000 цвята на базовото покритие и приблизително 1000 нови цвята се добавят към този списък всяка година. Стойност, т.е. , лекота или тъмнина, заедно с оттенък и наситеност на цвета, са стандартни термини, използвани индустрията, за да опише триизмерен характер на цвета е създаден с помощта на пигменти в базисна на превозното средство. Пигментите съдържат всякакви цветни, черни, бели или флуоресцентни твърди частици, които са неразтворими в боята, в която е вграден пигментът. Пигментите запазват кристалната или частичната си структура по време на процеса на оцветяване на основния слой. Ефектните пигменти включват алуминиеви люспи, микрофони и други. При пигментите с алуминиев люспест ефект, стойността или лекотата на покритието и разграничаването му между бяла, сива или черна скала зависи от ъгъла на наблюдение. С пигменти с ефект на слюда, нюансът, т.е. цветната класификация, зависи от ъгъла на наблюдение; този ефект се обозначава като цветен флоп. С различията в концентрацията на пигмент може да се промени цвета или наситеността на цвета, т.е. нивото на интензитет и богатство на цвета. Следователно, с различни пигменти и ефектни материали е възможно да се проектира неограничен брой автомобилни облицовки с уникални и отчетливи стойности, нюанси и цвят. За автомобили се използват три различни типа основни покрития, включително средни твърди частици (MS), високи твърди частици (HS) и пренасяни с вода. MS базовите покрития съдържат 15% -20% твърди нива и имат вискозитет на разпръскване 100 mPa.s при 1000 rpm. Основните покрития HS са разработени от основни покрития на MS. Водоносните базови покрития са се превърнали в основния основен слой, използван в цялата индустрия за производство на автомобили в САЩ от 2000 г. поради техните екологични ползи.
Крайното покритие върху повърхността на автомобила е прозрачният слой; той осигурява дълготрайност, устойчивост на околната среда и устойчивост на надраскване на цялостното покритие. Той предпазва от повреди като избледняване, причинени от UV лъчи от слънцето и придава блясък и дълбочина, които иначе не са толкова ярки. Прозрачното покритие също улеснява ремонтите и поддръжката.
Оформянето на околната среда е проблем, свързан с появата, свързан с образуването на постоянни водни петна или неотстраними следи от птичи изхвърляния, дървесна смола или други химикали след контакт с повърхността на автомобила. Физическите повреди са свързани с локализирана загуба на материал и деформация на повърхността на прозрачния слой. За да придадат UV устойчивост, химическите вещества HALS (препятстващ стабилизатор на аминовата светлина) се смесват с UVA (ултравиолетови абсорбатори на светлина) в автомобилни прозрачни покрития по време на тяхното производство. Основните функции на тези химикали са да предотвратяват разграждането на полимерния гръбнак (чрез HALS) и да абсорбират UV радиация в обхвата на дължината на вълната 290–400 nm. Показано е, че концентрацията на UVAs в прозрачните покрития намалява с около 50% след четири години излагане на слънце; това изчерпване е следствие от фотохимично разграждане и последваща дифузия от бистрата обвивка. HALS допълва активността на UVAs чрез пречистване на свободните радикали, които се образуват на повърхността на покритието, където UVA не могат ефективно да защитят полимера или в рамките на покритието с дължини на вълната, при които UVAs може да не абсорбира ефективно. Устойчивостта на надраскване на прозрачните покрития е друг фактор, който влияе върху дългосрочния вид на повърхността на автомобила. Някои фини драскотини могат да се видят само когато светлината се разсейва от самите драскотини; например, фините драскотини или разпръсквания, въведени от машините за автомивки, са следствие от леки деформации на повърхността, които могат да се изравнят във времето. Други драскотини причиняват отслабване или счупване на прозрачния слой. Характеристиките на потока и механичната издръжливост на прозрачните покрития зависят от това дали те са 1К (не изисква втвърдител, катализатор или активатор за втвърдяване) или 2К (трябва да се смесва с втвърдител, катализатор или активатор, за да се втвърди). 1K прозрачните покрития са показали по-висока устойчивост на потока от пластмаса, а 2K прозрачните покрития обикновено са показали по-висока счупване и по-твърда устойчивост на удар. Течните прозрачни покрития са най-доминиращата форма в световен мащаб, тъй като техниките за нанасяне, както и химията, са добре разбрани и оптимизирани; те също имат отлични показатели за автомобилно покритие. Химичният състав на течните прозрачни покрития варира до известна степен в зависимост от различните нужди на пазара или спецификации на клиента, но почти всички системи се основават на основи от акрилна смола, които са стабилни по време на съхранение и работа при стайна температура. Прозрачното покритие от 1K акрилен меламин е най-разпространената боя, използвана в автомобилната промишленост поради добрия си баланс на разходите и производителността. Обикновено се основава на комбинация от акрилни полиоли (Ac) и амино-омрежаващи агенти (MF, меламинови смоли). Версиите с прозрачно покритие с подобрена устойчивост на офорт и надраскване включват акрилен меламин силан и карбамат меламин. Както 1K, така и 2K полиуретановите прозрачни покрития също предлагат отличен баланс на устойчивост и надраскване, а прозрачните покрития от 1K и 2K епокси киселини са сред най-успешните търговски покрития по отношение на устойчивостта. Въпреки това, когато е формулирана като 1K система, срокът на годност на прозрачните покрития от епоксидна киселина е доста ограничен.Праховите прозрачни покрития стават все по-разпространени в автомобилната индустрия поради техните екологични ползи, т.е. липса на ЛОС по време на нанасяне. Освен това, те имат и други предимства, включително:
-
Директно рециклиране – свръхразпръскващ прах може да се събира и да се използва повторно в оригиналния процес на покритие;
-
Не се образуват отпадни води или утайки от боя по време на тяхното приложение;
-
Не е необходимо да се използват органични разтворители за почистване на оборудването за нанасяне или кабината за пръскане;
-
Намаляване на общата енергия, използвана по време на приложение, тъй като въздухът, подаван в кабината за пръскане, може да бъде рециклиран;
-
Не произвеждат ЛОС и много слабо токсични аспекти;
-
Еднакви дебелини на филма и подобрен вид на хоризонтални и вертикални повърхности.
Производителност на автомобилното покритие
Производителността на автомобилното покритие може да бъде оценена от различни гледни точки, например, трайността на облицовката на външна и вътрешна боя или естетическите характеристики. Съществуват обаче ограничения за свойствата на боята, възможностите на процеса и най-важното – сумата пари, която може да бъде изразходвана за подобряване на финала. Следователно всяка автомобилна компания определя стандартите си за цвят и външен вид, които трябва да отговарят или надвишават нивата, достигнати от конкурентите и очакванията на клиентите. Особено важно е еднаквостта или хармонията между всички компоненти.
Качество на покритието
Качеството на покритието могат да се преценят по три основни критерия: защита от тежки условия; трайност; и качество на външния вид Тежка среда се отнася до щети, причинени от падащи предмети, ултравиолетови (UV) лъчи, горещини (над 80 ° C) или студ (под -20 ° C), драскотини, скални удари (нарязване) и ръжда от сол или др. Мярка за издръжливост е да имате автомобил с устойчивост на ръжда над 20 години и добър цвят / блясък за повече от десетилетие. Трите параметъра за определяне на качеството на външния вид са цвят, гладкост на боята и блясък. Факторите, създаващи качество на външния вид, са визуално качество (естетика), определено от спрей покритието и включващо цвят и яркост и се влияе от наличието или отсъствието на метални люспи; външен вид (гладкост), което е свързано с неравностите на филма с дължина на вълната в обхвата от 1–5 mm; блясък, който е от значение за неравности с дължина на вълната 0,01–1,1 mm; и цветово и флопиращо изпълнение или способността на филма да показва свойствата за промяна на цвета в зависимост от гледания ъгъл.
Тенденции в процесите на автомобилно покритие
Прахово покритие
Едно от решенията за емисиите е подмяната на течните покрития с покрития под формата на сухи твърди частици, обикновено наричани прахови покрития. Съставите им съдържат много ниски концентрации на летливи разтворители от порядъка на 2%, значително по-малко от всяка друга бояджийска система. Понастоящем автомобилната индустрия използва прахово покритие на колела, брони, главини, дръжки на вратите, декоративни тапицерии и акцентни части, радиатори, филтри и многобройни части на двигателя. Разработен е и прозрачен прахов лак; BMW и Volvo го използват в новите си модели автомобили, а GM, Ford и Chrysler са сформирали консорциум, за да го тестват на производствените си линии. Праховите покрития са усъвършенстван метод за прилагане на декоративно и защитно покритие върху почти всеки тип метал и могат да бъдат използвани както от промишлеността, така и от потребителите.
Използваният прах представлява смес от фини частици пигмент и смола, която се разпръсква електростатично върху повърхността, която трябва да бъде покрита. Заредените прахови частици се прилепват към електрически заземени повърхности, докато прахът се нагрява и слее в гладко покритие в пещта за втвърдяване. Резултатът е равномерен, издръжлив, висококачествен и атрактивен завършек.
Праховите покрития отделят нулеви или почти нулеви ЛОС и могат да се използват за получаване на много по-плътни покрития от конвенционалните течни покрития без течане или провисване. Свръх-спреят може да бъде рециклиран, което означава, че е възможно да се постигне почти 100% ТЕ на покритието. Капиталовото оборудване и експлоатационните разходи за прахообразна линия са по-малко, отколкото за конвенционалните течни линии. Елементите, които са прахово боядисани, имат по-малко разлики във външния вид между хоризонтално и вертикално покрити повърхности, отколкото предмети с течно покритие. Също така, широк спектър от специални ефекти, които е невъзможно да се постигнат с други процеси на покритие, лесно се включва в праховите покрития. Въпреки че праховите покрития имат много предимства пред другите методи на покритие, има някои недостатъци на технологията.
Независимо от анти корозионния метод, който е приложен към автомобила, нито един от тях не е по-ефективен от сапуна и водата. Поддържането на автомобила ви чист и без замърсявания и мръсотия е най-сигурният начин да избегнете ръжда и корозия. Когато миете автомобила си, трябва да използвате и накрайник за пръскане под високо налягане, за да почистите ходовата част на вашия автомобил. Редовното миене и почистване на автомобила е най-добрият метод за предотвратяване на корозия. Той е и най-евтиният.